Leverage our exhaustive resources library, designed for your maintenance management needs.
Welcome to the TMA Systems resource library where you can explore all our knowledge assets on maintenance management and overall market trends and best practices.
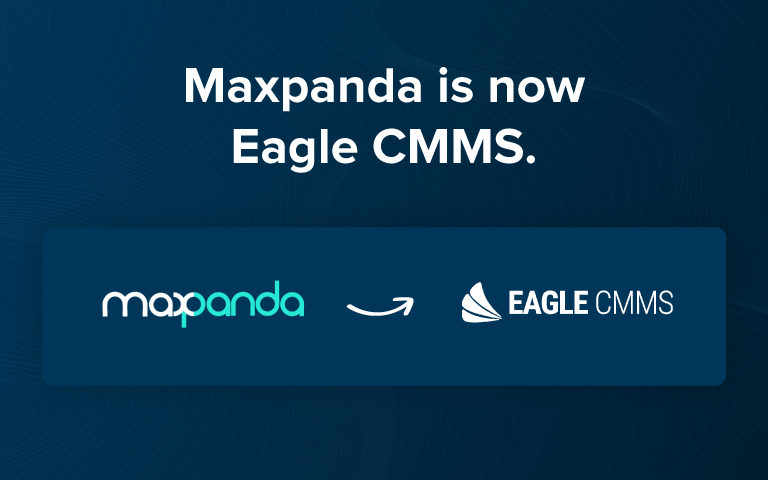
New Name, Same Commitment.
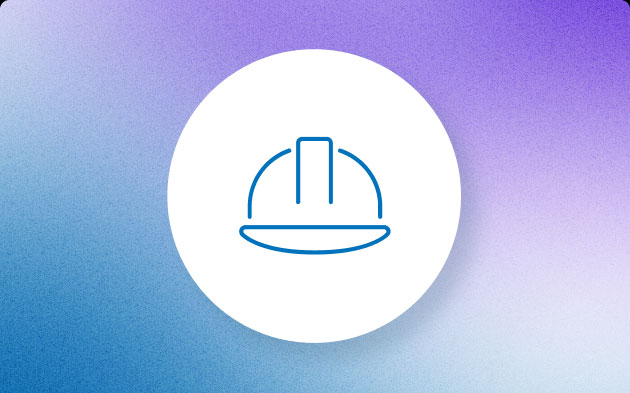
Revolutionizing Maintenance Management for K-12 Education with Eagle CMMS
The dynamic realm of K-12 education has one key foundation: excellence is non-negotiable, and every facility stands as a cornerstone in shaping young minds.
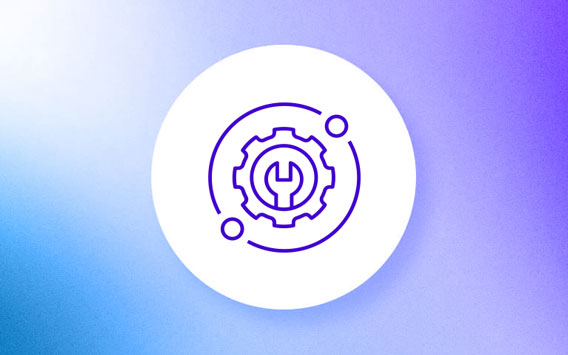
A guide to maximizing equipment life span using a CMMS
Equipment and assets that comprise an organization’s facilities are the lifeblood of operational success.
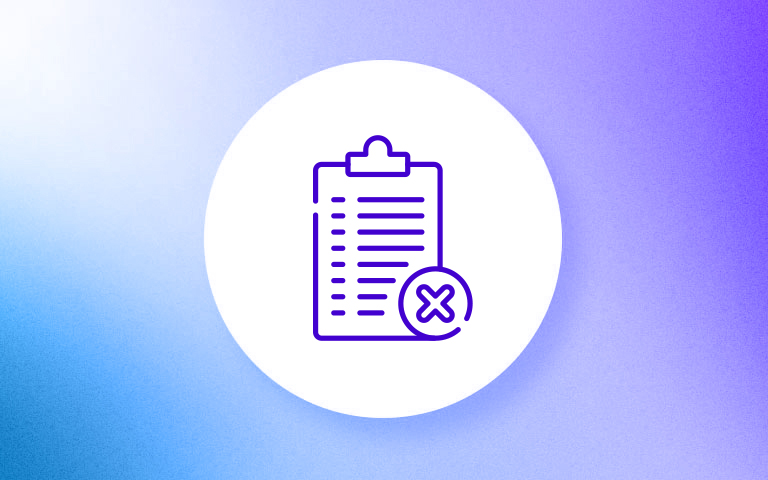
Common mistakes in MTBF analysis and how to avoid them
One of the best ways to avoid such events is to enhance asset reliability. A key metric used to assess equipment reliability is the mean time between failures (MTBF).
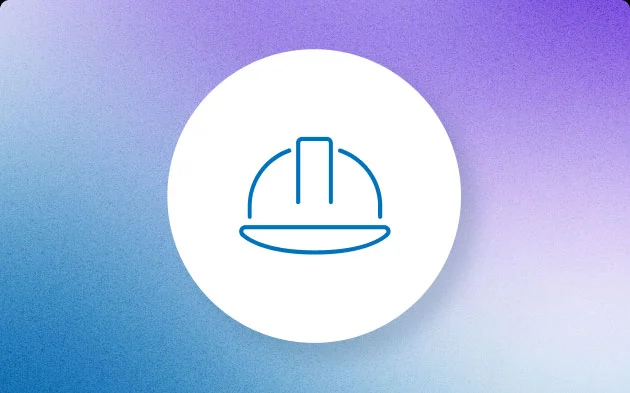
Understanding CMMS – What businesses need to keep in mind
A Computerized Maintenance Management System, often referred to as CMMS, serves as a comprehensive solution for streamlining maintenance operations, enhancing processes, and automating tasks to boost overall efficiency.
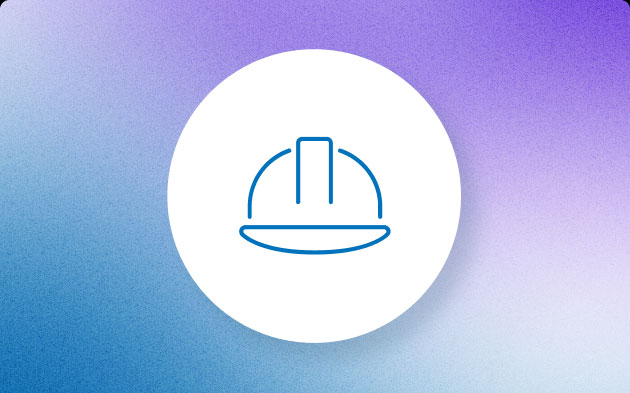
Efficient lubrication management - Key to higher equipment reliability
Adequate lubrication is a key factor for optimizing the performance of business-critical equipment for organizations of all sizes.
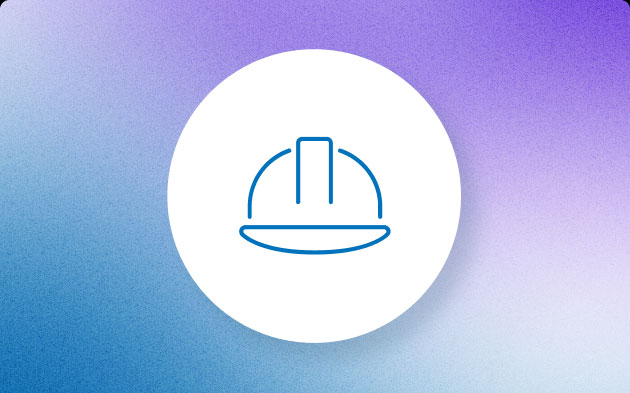
Utilizing key performance indicators for monitoring asset criticality
Three steps to enhance your maintenance program by determining the criticality of your organization’s assets using key performance indicators.
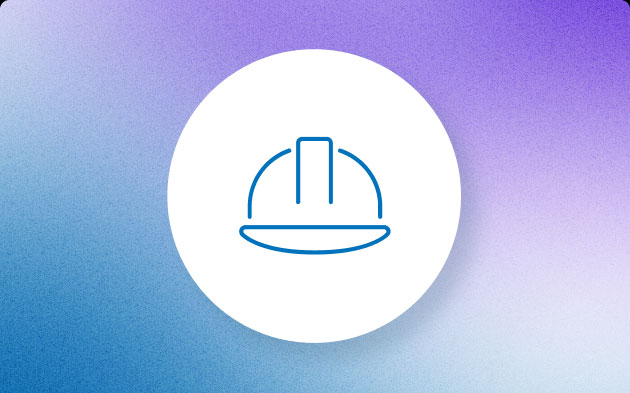
Three ways to reduce hospital facility maintenance costs
Adopting cost-saving strategies enable healthcare facility maintenance teams to enhance patients’, professionals’, and visitors’ experiences.
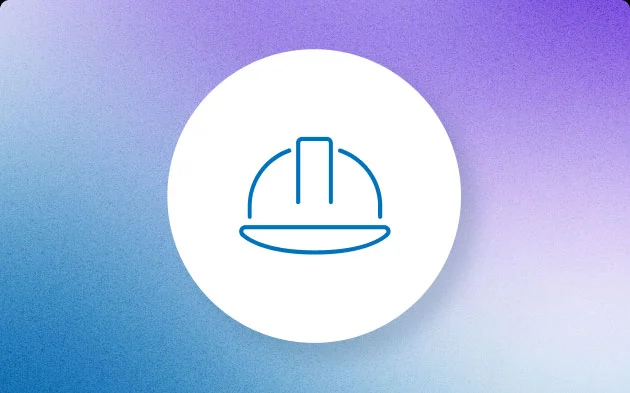
Achieving operational excellence through CMMS integration
Maximize the potential of your CMMS with enhanced efficiency and connectivity through universal interfaces and APIs. Utilize integrations for smooth business operations and ultimate efficiency.
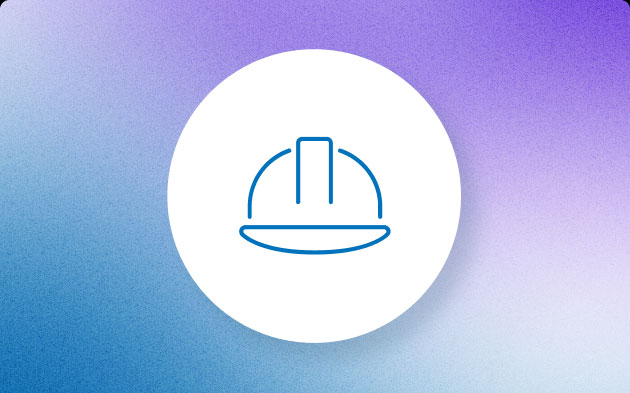
Role of MTBF in predictive maintenance strategies
MTBF represents the average time between failures or breakdowns of essential machinery and technological systems, originally pioneered by the aviation industry.
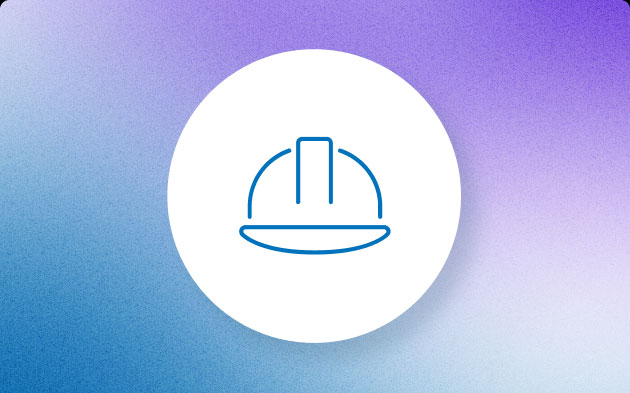
Maximizing CMMS efficiency through API integration
Seamless data sharing between a CMMS and other software improves maintenance accuracy and efficiency, enabling streamlined workflows and informed decision-making.
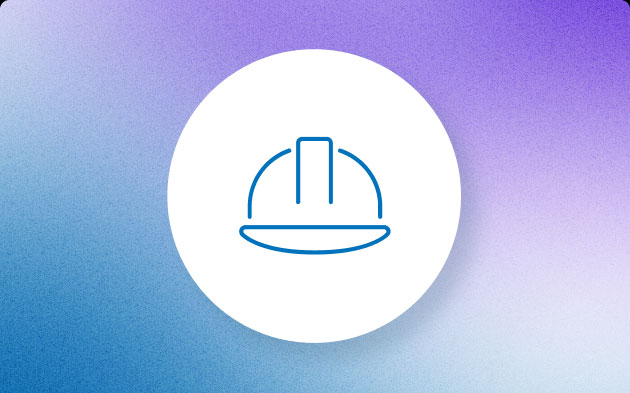
Modernizing supply chains by leveraging Industry 4.0 and CMMS
CMMS enables you to leverage Industry 4.0 optimally by harnessing the power of data and insights that comprise the core of the fourth industrial revolution.
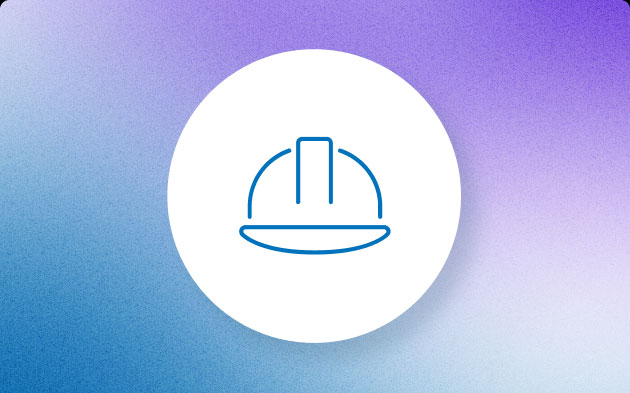
Revolutionizing healthcare maintenance: Four trends to watch
Advanced healthcare facility solutions improve efficiency, patient care, and outcomes through evolving technologies and optimized resource management.
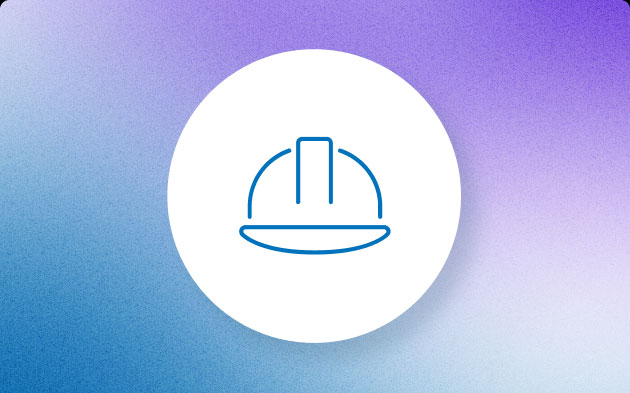
Best practices for CMMS preventive maintenance
Best practices to maximize CMMS preventive maintenance benefits to extend equipment lifespan and ensure operational continuity.
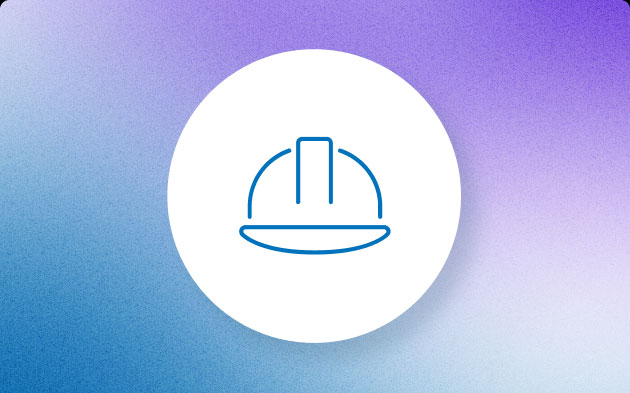
Best practices for asset maintenance management
Effective asset maintenance management maximizes productivity by eliminating production halts, costly repairs, and workplace hazards, dangers, and risks.
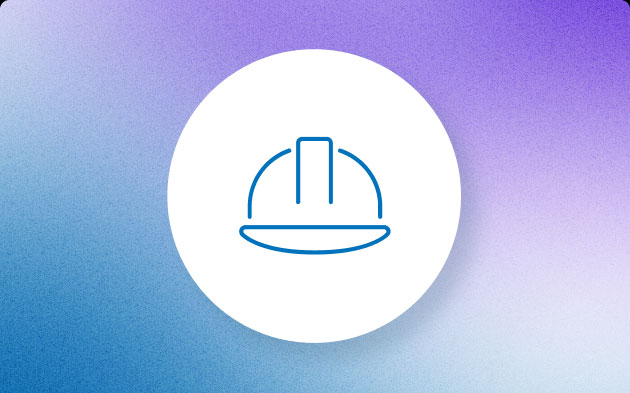
All you need to know about asset management solutions, in a nutshell
Effective asset maintenance is crucial for the success of any business that heavily relies on equipment, machinery, and other equipment.
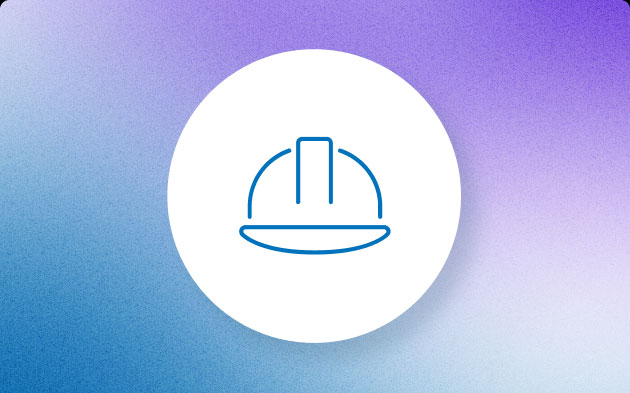
Embrace reliability-centered maintenance in 5 simple steps
Utilize an RCM approach to enhance operational efficiency and harness the benefits of proactive maintenance alongside your CMMS.
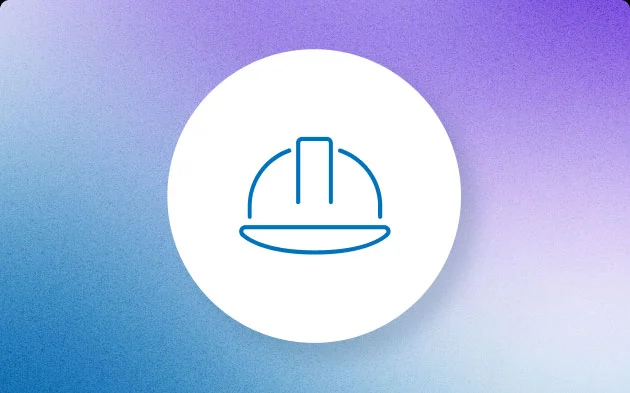
The Importance of Preventive Maintenance
Why Being Proactive with Preventive maintenance is Key to Equipment Reliability and Efficiency
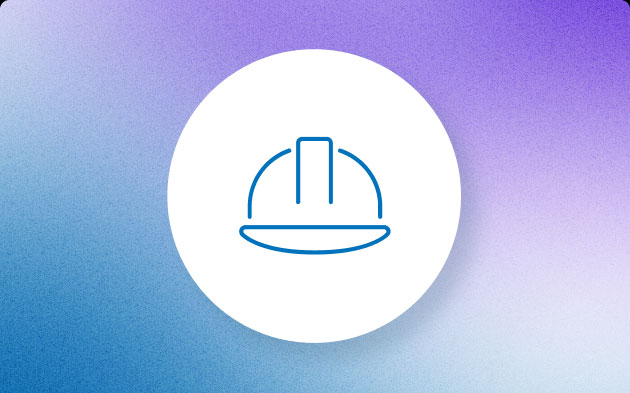
TMA Systems Welcomes Ed Roshitsh to Board of Directors
TMA Systems Welcomes Ed Roshitsh to Board of Directors
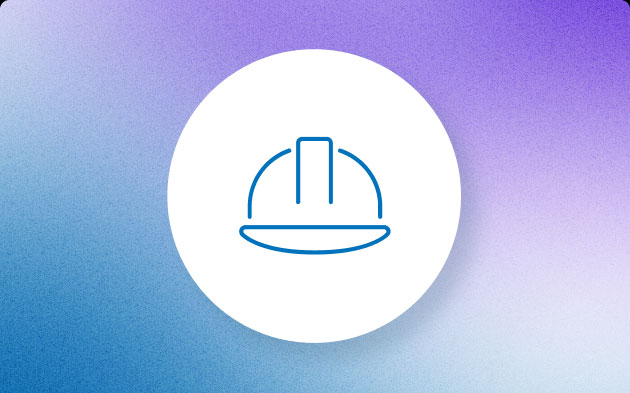
TMA Systems Acquires Maxpanda
Acquisition strengthens TMA’s market leadership with capabilities to service SMB to enterprise customers
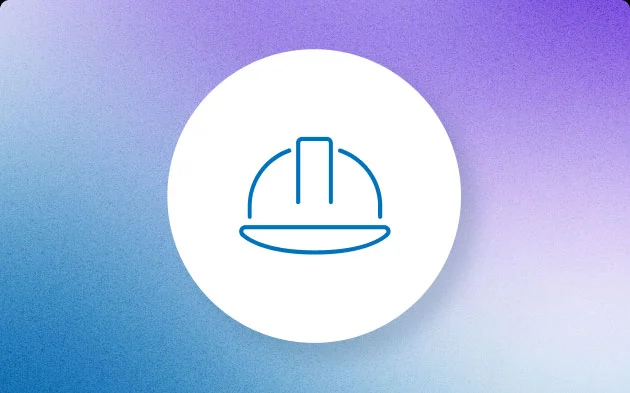
TMA Systems Acquires Prime Technologies
Acquisition extends TMA’s product offering by combining leading Calibration Management Software with the Company’s enterprise asset management suite
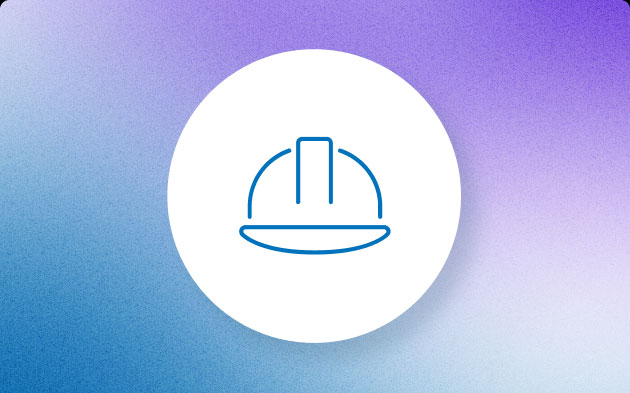
TMA Systems Adds Space Management Capabilities
TMA System’s partnership with ACAD-Plus allows data interchange with popular CAD systems to enable facilities managers to manage space more efficiently.
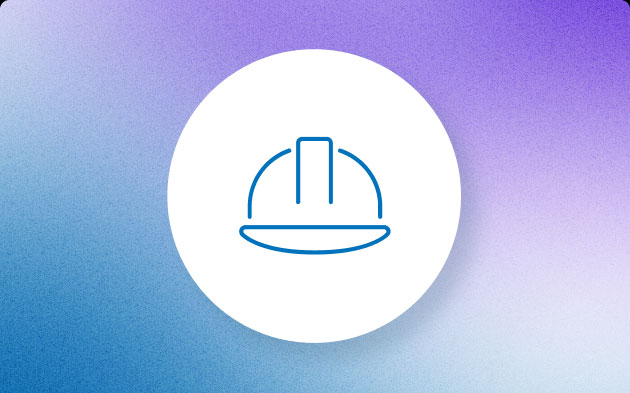
TMA Systems Appoints Mark Simner as Chief Executive Officer
TMA Systems, a world-class provider of advanced Computerized Maintenance Management Systems (CMMS) and Enterprise Asset Management Solutions (EAMS), today announced it has appointed Mark Simner as Chief Executive Officer.
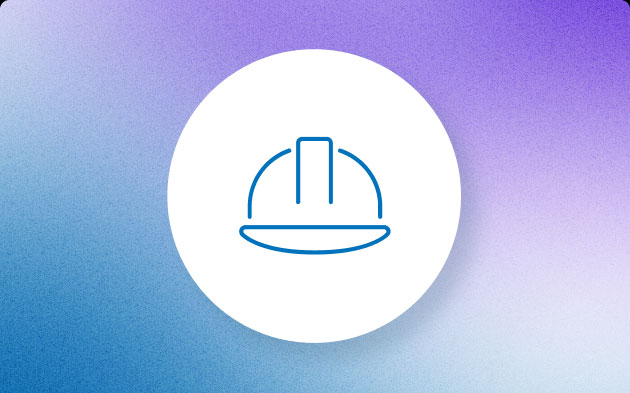
TMA Systems Raises $68 Million Growth Investment Led By Silversmith Capital Partners
TMA Systems, a world-class provider of advanced Computerized Maintenance Management Systems (CMMS), announced that it has secured a $68 million majority growth investment led by Silversmith Capital Partners, a Boston-based growth equity firm.
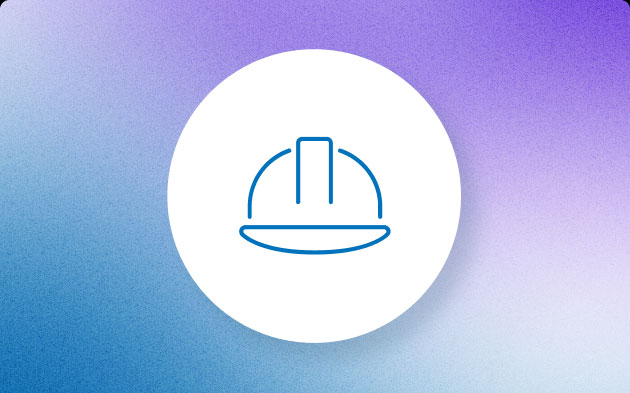
Study of Operational Maintenance Techniques
Effective operational maintenance is undeniably one of most obvious and cost-effective methods to ensure reliability, safety, and efficiency in enterprise operations.
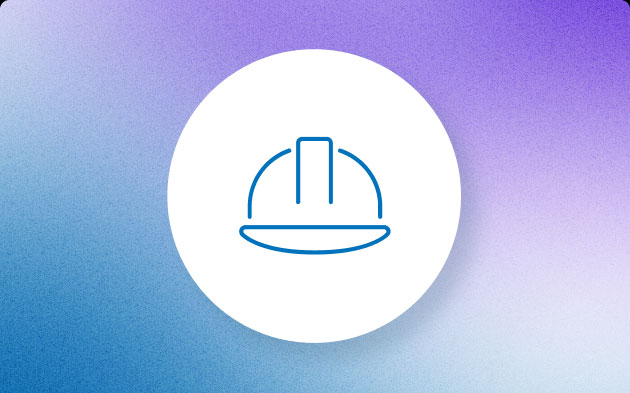
CMMS: Ushering in the Era of Cost-effective Maintenance
Maintenance can make or break operations. Enterprises often face challenges and consequences that range from poor quality output to declining safety standards.